
Business Process Mapping and Improvement
Why map business processes?
We use process maps to ‘tell the story’ of the operation we are looking at, and then to help describe how to make it work better. This is widely known as Business Process Improvement.
As most people prefer pictorial visualisation of concepts, we can tell the story using the process map in the form of a flow chart or flow diagram.
Process mapping also allows us to structure the story in chunks that can be better represented, understood and evaluated. In the same way as a book is structured into the book concept (title), the associated volumes (often only one), its sections, chapters and paragraphs, the flow of work through an organisation is equally represented by its business units, its regions, departments, functions, processes, procedures (work instructions), forms / templates / other information artefacts, and finally its data fields.
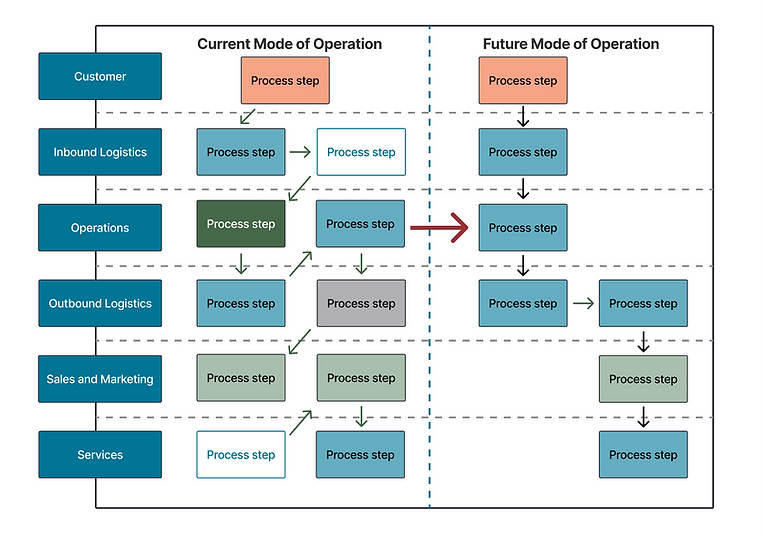
Our capabilities

Process mapping, process analysis, process redesign, process standardisation

Business Process Management

Process Improvement

Process cost and FTE analysis

High level Business Requirements definition
Facilitated workshops
Process mapping and modeling tools (eg BizAgi Modeler, Holocentric Modeler)
Workflow simulation software
The tools we use
Our approach
Outcomes

Improved throughput
Organisations wishing to increase their throughput rates need to consider two questions beforehand. One, will their market buy the additional items they deliver? And two, is there sufficient financial benefit in delivering the extra items in the first place? If both the answers are `yes’, then throughput improvements are a meaningful goal.

Improved margin
Margin in a business is often expressed as a percentage of revenue. In many cases it is applied at many levels including gross profit, net profit, contribution etc. In all these cases it is a measurement of a value, typically profit within a context of an industry accepted formula.

Reduced operating costs
Operating costs, often referred to as OPEX, is the category of expenses in a business that occur as a result of its normal business operations. A key objective in what we deliver is to assist management in determining how operating expenses can be reduced without significantly affecting the business’ ability to compete.

Improved return on assets
Assets in a business are often expressed as items of economic value to that business, for example: cash, inventory, equipment, computer systems, real estate, goodwill, patents etc. Assets in an accounting sense fall into tangible (physical and measurable) and intangible (conceptual and complex to measure).
Our recent clients


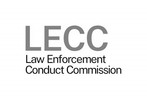

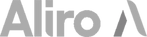
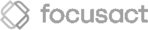
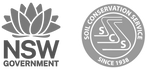
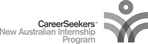
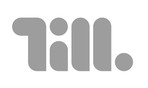
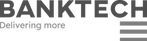
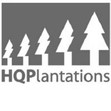
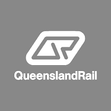


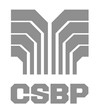
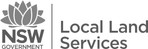





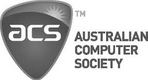

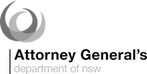
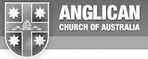
The right start makes all the difference to your project
One of the biggest causes of failure for change programs is the lack of understanding of the issues, by all stake holders. It is not uncommon for sponsors to adopt the approach of ‘we know what the problems are, now just fix them’. This is starting from Stage 2; ‘we know what we don’t know’.
This approach will certainly gloss over the root causes of the issues and alienate the people dealing with those issues on a day to day basis and whose support is vital for the resolution of each issue.
Our approach ensures our clients start from the position of ‘we don’t know what we don’t know’ (Stage 1), and in doing so, maximise the return from their investment in change.
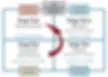
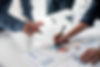